08.28.2024 | Global Miami Magazine
In partnership with a Turkish investor, RENCO brings a new way to build in the U.S.
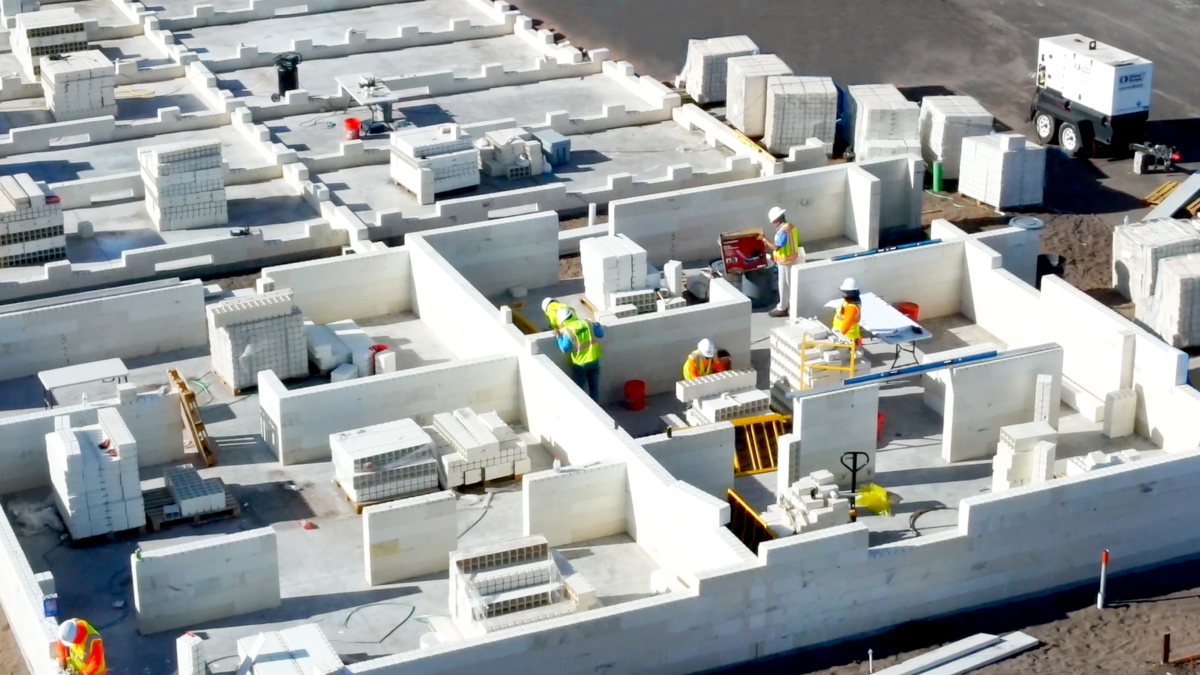
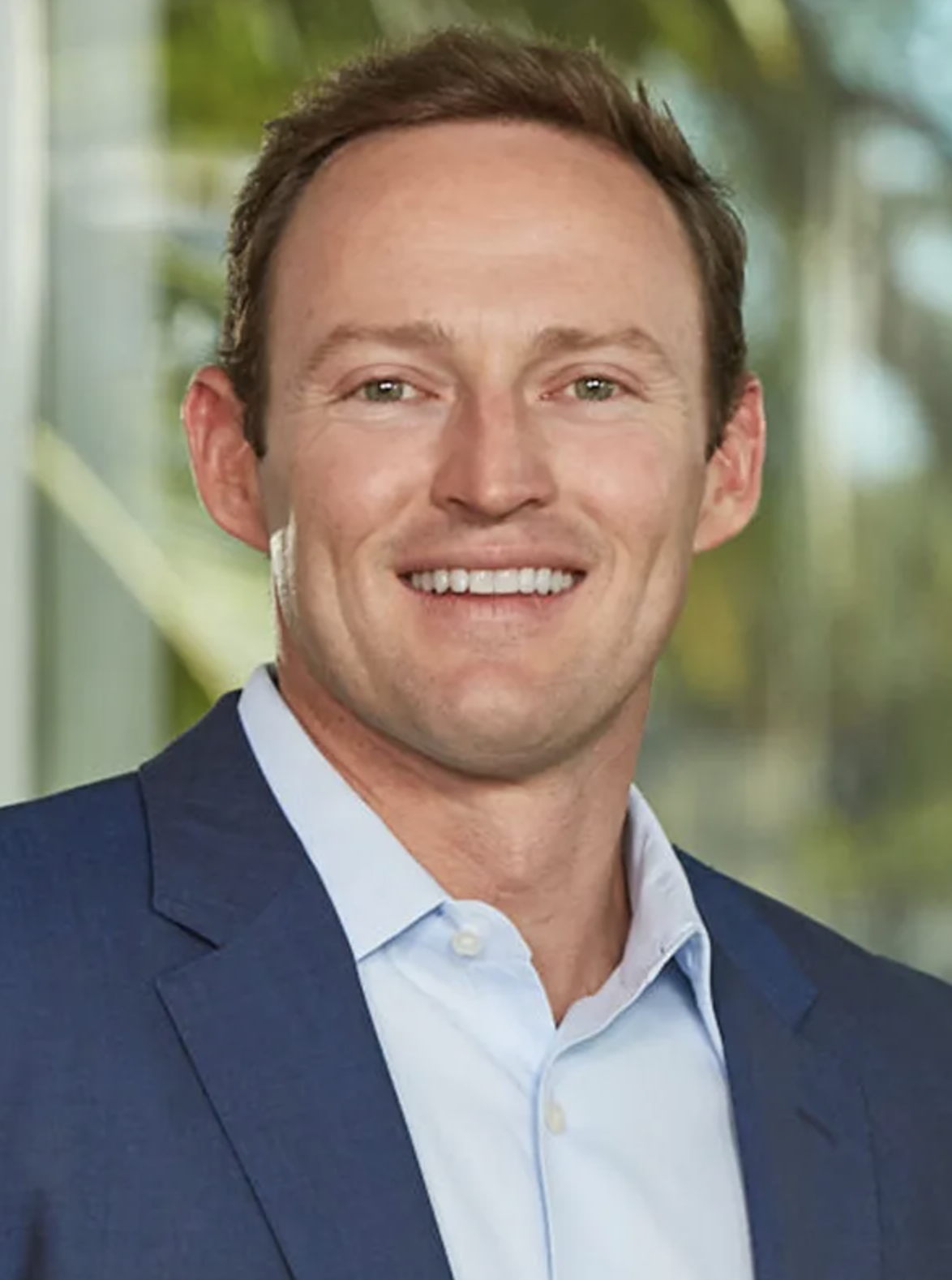
While RENCO USA was founded in 2012, its materials had been used by RENCO Global in Turkey since the previous year. The material was created to help the country rebuild faster after earthquakes, and it’s now used in Iraq, Syria, and other Middle East countries. RENCO USA has been importing its materials from the original factory in Manisa, Turkey, but it will soon open a factory in Palm Beach County capable of producing enough blocks to build 6,000 apartment units per year.
RENCO’s blocks are both less expensive than traditional materials and greener. According to the Athena Sustainable Materials Institute, a non-profit that researches the carbon footprint of construction, RENCO materials contain 82 percent less embodied carbon than structural steel and 62 percent less embodied carbon than reinforced concrete. The blocks are also lighter than their concrete counterparts, thus requiring less energy and fewer vehicles to transport. Murphy says that for every truckload of RENCO’s composite materials, it takes four trucks to deliver the same quantity of concrete block.
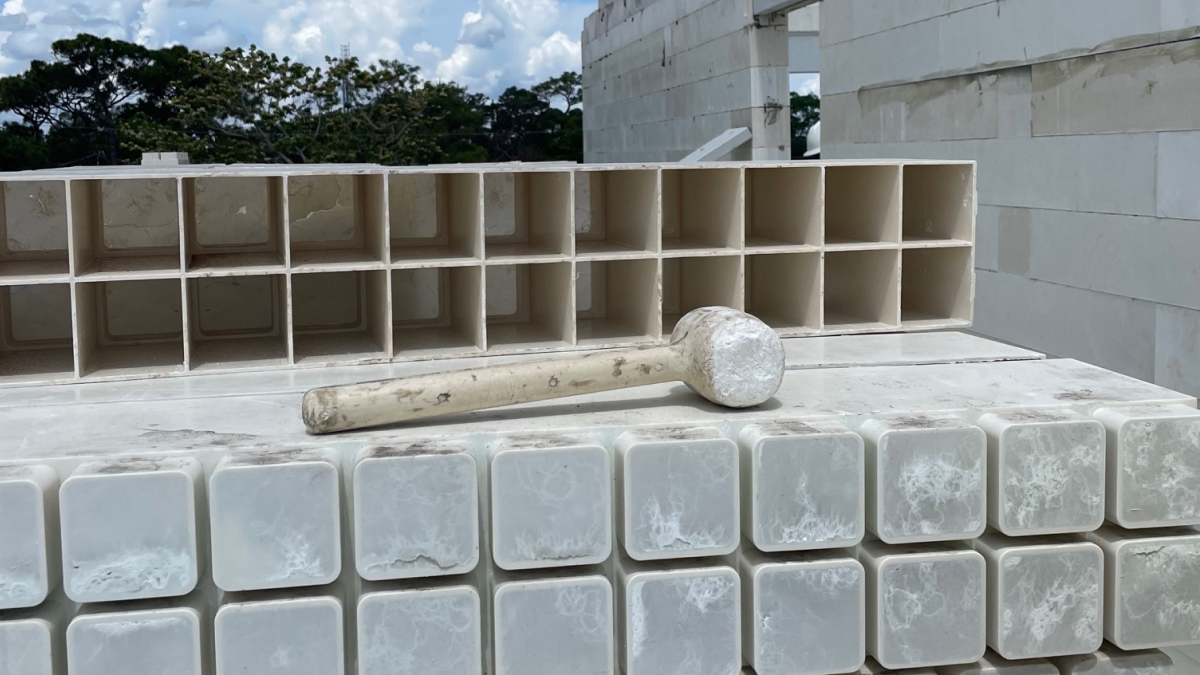